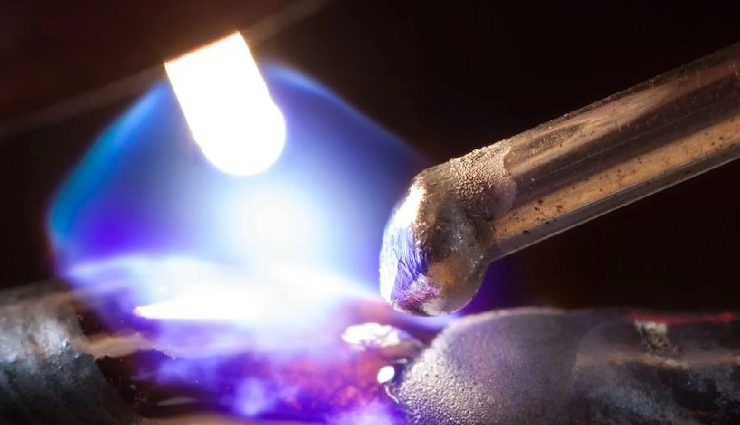
Welding is a vital process in various industries, from construction to automotive manufacturing. Achieving welding excellence requires attention to detail, and the right tools. However, one crucial component that often goes overlooked is the choice of shielding gas. This article tells you how the right shielding gases can significantly impact welding quality and provide valuable insights for buyers.
Role of Shielding GasShielding gas plays a pivotal role in the welding process, especially in techniques such as MIG (Metal Inert Gas) and TIG (Tungsten Inert Gas) welding. Its primary function is to protect the weld pool from atmospheric contaminants, such as oxygen, nitrogen, and moisture, which can compromise the quality of the weld.
Gas Composition MattersThe composition of shielding gas is not one-size-fits-all. Different welding applications require specific gas blends to achieve optimal results. Buyers need to be aware of the following gas compositions:
Argon: Widely used for TIG welding, argon provides excellent arc stability and is ideal for non-ferrous metals like aluminium and copper.
Carbon Dioxide (CO2): Often used in MIG welding, CO2 enhances weld penetration and is suitable for welding carbon steel.
Argon-CO2 Mix: A blend of argon and CO2 offers versatility and is suitable for a wide range of metals, including stainless steel and mild steel.
Helium: Helium is used for high-heat applications and is commonly employed in TIG welding of thick materials.
Oxygen: Oxygen can be added to the mix in small amounts for improved arc stability, particularly in MIG welding.
Gas Purity and QualityBuyers should prioritise the purity and quality of the gas. Even a small amount of contamination can lead to weld defects. Ensuring that the gas supplier adheres to strict quality standards is essential. High-quality shielding gas should have minimal impurities and moisture content.
Tailoring Shielding Gas to Welding ApplicationsThe choice of gas should align with the specific welding application. Here are some insights into tailoring your gas selection:
Material CompatibilityDifferent metals require different shielding gas for optimal results. For example, stainless steel welding benefits from a tri-mix gas blend (argon, helium, and CO2), while aluminium welding necessitates pure argon or an argon-helium blend.
Welding TechniqueConsider the welding technique being used. MIG welding, for instance, often relies on a mix of argon and CO2 for versatility, while TIG welding primarily uses argon due to its stability.
Thickness of MaterialThe thickness of the material being welded impacts gas selection. Thicker materials typically require higher gas flow rates to ensure adequate protection and penetration.
Gas Flow Rate and PressureProper gas flow rate and pressure are critical factors in achieving welding excellence. Buyers should be aware of the following considerations:
Flow RateThe gas flow rate is typically measured in cubic feet per hour (CFH) or litres per minute (LPM). It should be adjusted based on the welding process, material thickness, and nozzle size. Too much gas can lead to turbulence, while too little can result in insufficient protection.
Gas PressureMaintaining the right gas pressure at the regulator is crucial. This pressure ensures a consistent flow of gas to the welding torch. Buyers should consult welding charts and guidelines to determine the appropriate pressure settings for their specific welding application.
Storage and HandlingProper storage and handling of shielding gas cylinders are essential to maintain gas quality and safety. Buyers should take note of the following:
Storage ConditionsShielding gas cylinders should be stored in a cool, dry, and well-ventilated area away from direct sunlight and heat sources. Proper storage prevents contamination and ensures gas stability.
Cylinder HandlingWhen transporting or changing gas cylinders, buyers should exercise caution to avoid dropping or mishandling them. Damaged cylinders can lead to leaks and safety hazards.
In the welding world, it's essential to always strive for excellence. As a buyer, you can contribute to this by making smart choices when it comes to picking the right shielding gas. By choosing the right shielding gases, you can improve your welding results and achieve better outcomes. So, take the time to learn about these gases and their applications to make the most informed decisions for your welding projects.